Keep Your MDR Conveyor System in Check with This Guide!
Motor Driven Roller (MDR) conveyor systems are a game-changer for material handling. They’re energy-efficient, quieter than traditional conveyors, and give you precise control over product movement. But like any piece of equipment, MDR conveyors can run into issues. When they do, knowing how to troubleshoot the problem can save time, money, and a lot of frustration.
MDR conveyor maintenance is key to keeping your system running smoothly. Regular upkeep helps prevent conveyor system issues before they start. But even with the best maintenance, things can still go wrong. That’s where knowing a few conveyor troubleshooting tips can make all the difference.
Let’s break down the most common MDR conveyor problems, how to fix them, and when to call in the experts at Russell Conveyor & Equipment.
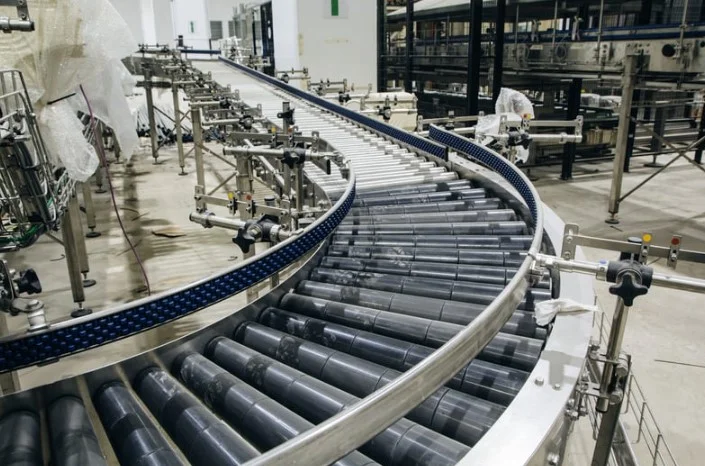